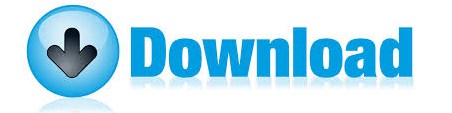

The design of MPC is based on mathematical model of an object (relatively simple). The purpose of the paper is to design and analyse control system of carbon monoxide oxidation in the convector cavity based on MPC with linear-quadratic cost functional with constraint. These advantages allow managing multidimensional objects with a complex structure, including nonlinearity, optimizing processes in real time within the constraints on controlled and managed variables, taking into account uncertainties in the task of objects and perturbations. Model predictive control (MPC) approach is the basic feedback scheme, combined with high adaptive properties, which determines its successful use in the practice of design and operation of control systems. Model predictive control, linear-quadratic cost functional, state space model, control system Abstractīackground. Igor Sikorsky Kyiv Polytechnic Institute, Ukraine Please remember to properly cite other software that you might be using too if you use do-mpc (e.g. Control Engineering Practice, 60:51-62, 2017 Rapid development of modular and sustainable nonlinear model predictive control solutions. If you use do-mpc for published work please cite it as: Please visit our extensive documentation, kindly hosted on readthedocs. Installation instructions are given here. The development is continued at the Laboratory of Process Automation Systems (PAS) of the TU Dortmund by Felix Fiedler and Sergio Lucia.
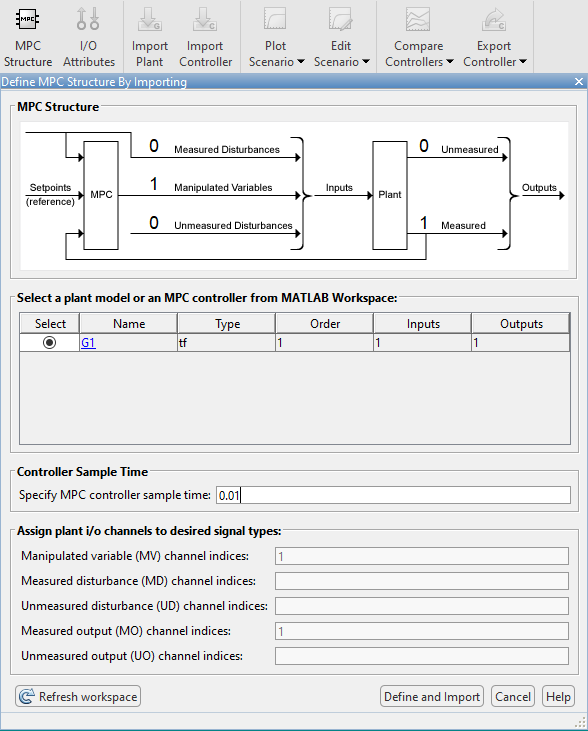
do-mpc has been developed by Sergio Lucia and Alexandru Tatulea at the DYN chair of the TU Dortmund lead by Sebastian Engell. The do-mpc software is Python based and works therefore on any OS with a Python 3.x distribution.
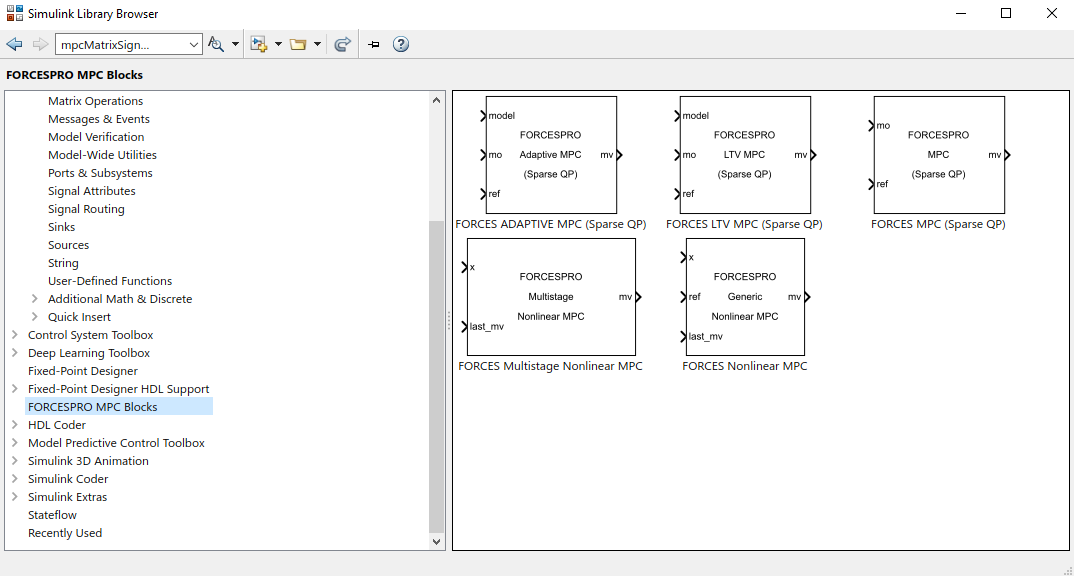
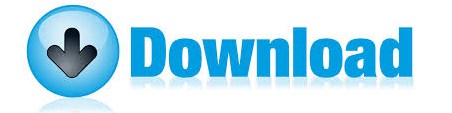